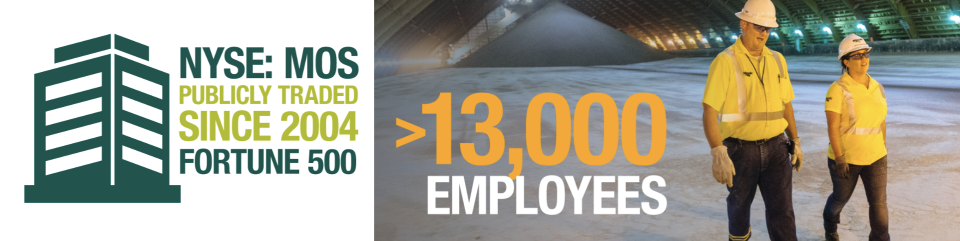
The Mosaic Company (NYSE: MOS) is the world’s leading integrated producer of concentrated phosphate and potash—two of the three most important nutrients in agriculture. We employ more than 13,000 people in six countries to serve farmers all over the world. Our Headquarters is in Lithia, Florida with operations throughout North America (U.S./Canada) and South America.
At Mosaic We Help the World Grow the Food it Needs - Apply today and join our team!
Where will you work: Onsite Lithia, FL
As core member of our Operations Technology (OT) Advanced Process Controls (APC) team, the Operations Lead is responsible for ensuring the successful implementation of new process control technological solutions within our operations.
This role provides critical coordination with the operations team customers and ensures APC solutions are practically implemented, that appropriate preventative maintenance plans are created, and that customer teams are appropriately trained and supported.
The APC team, and this role, work primarily in an Agile approach with a scheduled sprint cadence that is coordinated with site operations/automation teams. This team manages all steps to implement automated solutions from inception to verified functional product.
What you’ll do?
- Collaborate within the APC team to brainstorm and design control philosophies that ensure practicality, ease of understanding, and effective troubleshooting. Enhance process safety, stability, reliability, cost-efficiency, and throughput related to APC solutions.
- Conduct operator training, develop lifecycle asset management requirements, and create standing PM’s for APC critical equipment. Execute management of change procedures.
- Work alongside the APC Process Control Engineer to implement control schemes, alarms, interlocks, and safety permissive.
- Coordinate the on-site installation of new assets critical to the deployment of APC solutions.
- Interface with the local operations group to properly schedule the commissioning of APC solutions. Provide troubleshooting support.
- Collaborate with the Process Engineer to leverage data historian asset frameworks for implementing SPC visualization. Assist in quantifying the financial gains from implemented solutions.
- Collaborate with APC team members to troubleshoot in-field components.
- Ensure appropriate maintenance, scrub cycles, and PMs are set to occur on critical assets to sustain APC solutions.
- Work with the APC team to identify and procure the required hardware and software components to achieve the outcome of the automated solution.
- Collaborate with APC team members to estimate the time required to complete the backlog of tasks.
- Other job duties as assigned.
What you’ll need:
- Bachelor’s Degree in Engineering, required.
- 5+ years in industrial operations or engineering role
- 5+ years working with process controls, ICS systems, automation systems.
- Strong operational background with proven track record of driving operational change to optimize processes
- Microsoft Office Suite; Microsoft Power BI
- Experience with Process Control Systems and HMI experience; Data historian and visualization experience.
- 10% travel required
Knowledge, Skills, & Abilities: Excellent facilitation, communication, and team-building skills; Ability to work with employees at all levels of the organization; Demonstrated problem solving and analytical skills; Ability to work as part of cross-functional and collaborative team; Experience in Agile work processes; Interpret electrical diagrams and P&ID’s
Bonus if you have the following:
- Certifications: Preferred - Agile certification(s)
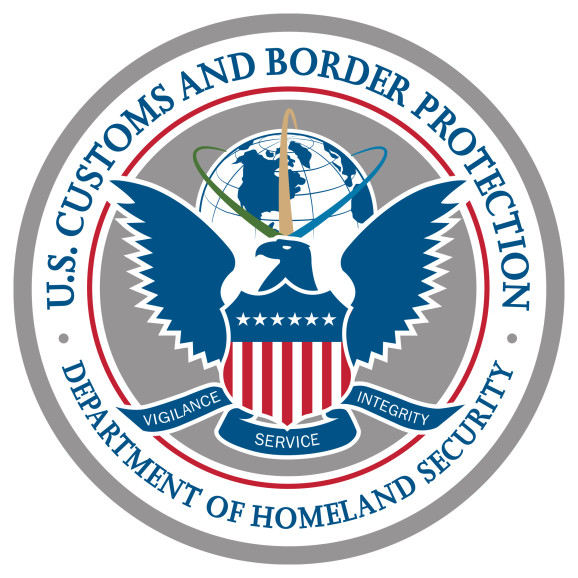